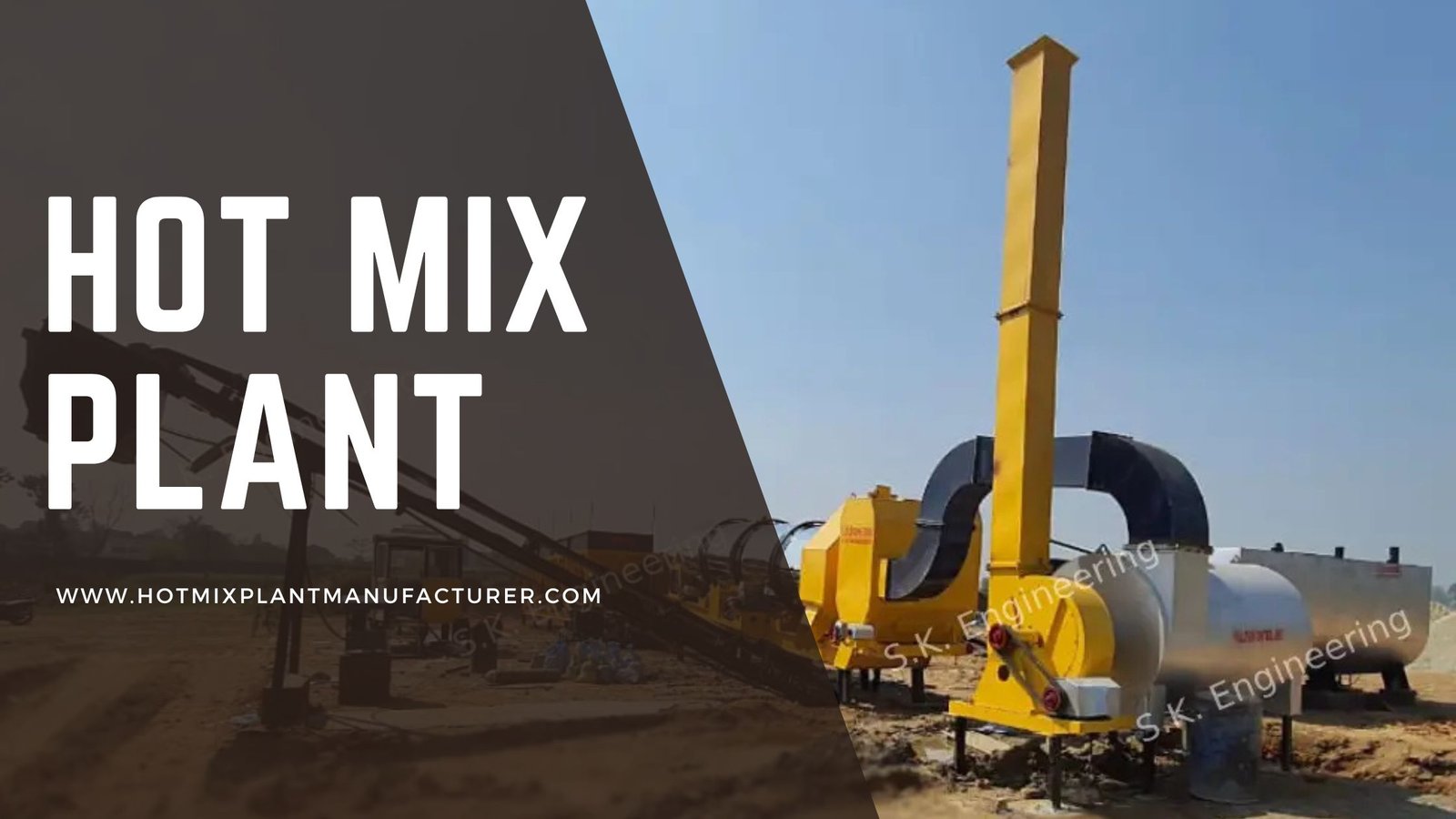
India’s infrastructure is rapidly evolving, with a significant focus on road development and highway construction. At the heart of this transformation lies the Hot Mix Plant—a vital piece of equipment that plays a central role in producing the bituminous mixture essential for paving roads. As demand for efficient, high-quality construction rises, so does the need for reliable and advanced hot mix plant manufacturers.
In this blog, we dive into what makes a top-tier hot mix plant manufacturer, how hot mix plants function, and what buyers should look for when investing in one for their road construction projects.
What is a Hot Mix Plant?
A Hot Mix Plant (HMP) is a piece of heavy machinery designed to mix asphalt, aggregates, sand, and filler materials with bitumen at elevated temperatures to produce hot mix asphalt (HMA). This asphalt is used to construct roads, highways, and parking lots.
There are two major types of Hot Mix Plants:
- Batch Mix Plant – Mixes asphalt in batches; offers more control and flexibility.
- Drum Mix Plant – Continuous mixing plant; ideal for larger, high-volume projects.
How Does a Hot Mix Plant Work?
While variations exist across manufacturers and plant models, the typical process in a hot mix plant includes:
- Feeding Cold Aggregates into bins.
- Drying and heating them in a rotary drum.
- Mixing with Bitumen and Filler inside a mixer (batch/drum).
- Storage in Silos or direct discharge into trucks.
The goal is to produce a homogeneous asphalt mix with consistent temperature and distribution of materials.
Role of a Hot Mix Plant Manufacturer
A reputable hot mix plant manufacturer doesn’t just build equipment—it supports the entire lifecycle of your road construction project. From designing robust plants that meet specific project needs to offering after-sales service, spare parts, and on-site installation, the right manufacturer is a long-term partner in infrastructure success.
Why Choosing the Right Manufacturer Matters
Customized Plant Designs
Every road project has unique requirements. Reliable manufacturers provide custom configurations—from small capacity mobile plants to large stationary batch mix plants.
Quality Components
High-grade steel, precision-engineered drums, wear-resistant liners, and advanced burner systems make a huge difference in durability and performance.
Automation & Technology
Today’s top manufacturers equip hot mix plants with PLC-based control systems, real-time monitoring, and dust collection systems to enhance productivity and environmental compliance.
Fuel Efficiency
Advanced heating systems, efficient burners, and insulated drums reduce fuel consumption, lowering operational costs.
Environmental Compliance
Leading manufacturers ensure their equipment complies with pollution control norms, incorporating dust collectors, bag houses, and emission reduction technologies.
Training & Support
Beyond installation, good manufacturers provide operator training, troubleshooting guides, and 24/7 support for seamless plant operation.
Applications of Hot Mix Plants
- National Highway Development Projects
- State Road & Rural Infrastructure
- Airport Runways
- Urban Road Resurfacing
- Private and Industrial Road Construction
Factors to Consider Before Buying a Hot Mix Plant
- Production Capacity: Measured in tons per hour (TPH); choose based on project scale.
- Portability: Mobile plants for temporary sites; stationary for large, long-term works.
- Automation Level: Manual, semi-automatic, or fully automatic controls.
- Fuel Options: Diesel, natural gas, or coal, depending on availability and budget.
- Ease of Maintenance: Plants with modular components and easy servicing access reduce downtime.
- Warranty & Service: Check for manufacturer warranty, spare availability, and proximity of service centers.
What Sets a Trusted Hot Mix Plant Manufacturer Apart?
- ISO-certified production
- Use of branded electrical & mechanical parts
- Decades of industry experience
- On-time delivery & commissioning
- Client list with major infrastructure firms
- Export capabilities for overseas projects
Conclusion
The quality and efficiency of a hot mix plant directly influence the speed, quality, and cost of road construction. Choosing the right hot mix plant manufacturer is not just about buying a machine—it’s about investing in a reliable partner that ensures your project is completed on time, within budget, and up to the highest industry standards.
Whether you’re building a rural road or a major expressway, working with a proven manufacturer is key to long-term success in infrastructure development.
FAQs: Hot Mix Plant Manufacturer
Q1: What is the average cost of a hot mix plant in India?
Prices vary based on capacity, type (batch or drum), and features. Entry-level plants may start at ₹25–30 lakhs, while larger, fully automated plants can exceed ₹1 crore.
Q2: How long does it take to install a hot mix plant?
Installation typically takes 2–4 weeks, depending on plant size, site conditions, and manufacturer support.
Q3: What is the lifespan of a hot mix plant?
With proper maintenance, a quality plant can operate efficiently for 10–15 years or more.
Q4: Can I use recycled asphalt (RAP) in a hot mix plant?
Yes, some advanced models allow RAP integration, helping reduce material costs and promote sustainability.
Q5: Do manufacturers offer AMC (Annual Maintenance Contracts)?
Top manufacturers offer AMC packages to ensure optimal performance and minimal breakdowns.